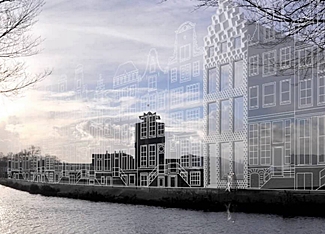
Imagine constructing a new home from start to finish in just 10 days – a process that would normally take at least six months and involve a very large amount of manpower.
Far from being a dream it is already a reality thanks to the rise of 3D-printing which is making waves across the world. Since the first houses were printed in China last year, many other engineers have been experimenting with the technology – from the world’s first 3D-office in Dubai to the world’s first 3D-printed canal house in Amsterdam.
Asia has also been swept up by the trend, particularly because of its potential to shrink construction budgets and timelines. It also has the potential to provide affordable homes for low-income communities. In Thailand, providing low-cost homes for low-income earners is also a very hot topic, and a prime mission for the government.
This idea has already struck a chord with the Philippines government after Lewis Yakich, a material science engineer from California who owns the Lewis Grand Hotel in Angeles City unveiled the world’s first 3D-printed hotel suite.
His 130-sqm, two-bedroom villa took about 100 non-consecutive hours to print (including a 3D-printed Jacuzzi) and he has big plans to scale up his 3D-printed buildings to include low-income homes in the Philippines.
“I locked down a Memorandum of Agreement to start pre-selling 200 low-income homes,” Yakich told 3DPrint.com.
“The goal would be to expand to 2,000 homes within two years. The Philippines is in such need of low-income housing that this technology is perfect for it.”
He estimates 3D-printing could save around 60 percent on traditional building costs.
JLL’s Manila-based Local Director of Project and Development Services Kiko Abarquez isn’t surprised by how the Philippines is embracing the technology.
“Filipinos, in general, are tech fanatics,” he said.
A model for the future
The former architect also said it could prove valuable in the aftermath of natural disasters, building existing technology was employed after Typhoon Haiyan.
3D-printing addresses the issues of speed of delivery and immediate occupancy and “none of the occupants [disaster victims] would really care about defects” that would likely occur in a project during the experimentation stage, Abarquez explained.
However he believes 3D-printing is still received with much skepticism within the industry.
“After all, it is being introduced in an industry that has been used to labour-intensive projects and traditional approaches that have been tested with time,” he said.
“If there is a faction of the industry that will likely take this on, it will be the large local developers who have got a huge pipeline of projects, both in the commercial and residential markets, and have the best opportunity to experiment.”
Abarquez added he can “see a lot of opportunities to have this technology adapted specifically on off-site fabrication of common elements and external building cladding elements”.
But ultimately, given the huge upfront investment, the decision would come down to “how quick the return on investment would be”.
3D-print designer Andrey Ruchenko, who worked with Yakick on the hotel project. believed that while the large scale 3D-printing of buildings is still a work in progress, it has huge potential.
“The assembly time for the first printer was two months but this can be replicated now within a couple weeks as the assembly process has been worked out,” Rudenko told 3Dprint.com.
“It took approximately one month to develop and test the right mix, using local materials. We have sand with volcanic ash in the Philippines, which is difficult to extrude, but a reliable process was developed and we obtained great results with pretty strong walls and good bonding between layers.”
It may be early days for 3D-printing but with high interest levels and competition in the industry, the next few years could herald big changes in the way homes are constructed both in the Philippines and elsewhere.
This article was first published by JLL on their www.jllrealviews.com website and is reproduced with kind permission.